Dealership Info
send us a message
read our FAQ's
Premature oil seal failure can result from improper installation, poor shaft finish, incorrect material selection, or excessive pressure. To prevent this, ensure the shaft surface is smooth and within tolerance, use correct tools during installation, and choose seals made from materials compatible with your media and temperature.
Always clean the shaft and bore before installation. Use appropriate seal drivers to avoid deformation. Lubricate the lip before fitting to reduce friction during the first rotation. Ensure the seal is seated evenly and not tilted to avoid leaks.
Check if the pressure exceeds the seal’s rated limit. Examine for wear, hardening, or improper installation. Replace the seal if damaged, and consider upgrading to a high-pressure CFKS seal variant. Also, verify that the housing and shaft are properly aligned.
For high temperatures, aggressive chemicals, or abrasive environments, choose CFKS seals made of FKM, PTFE, or high-performance elastomers. Consider using seals with protective dust lips or metal casing. Our team can recommend the best fit for your application.
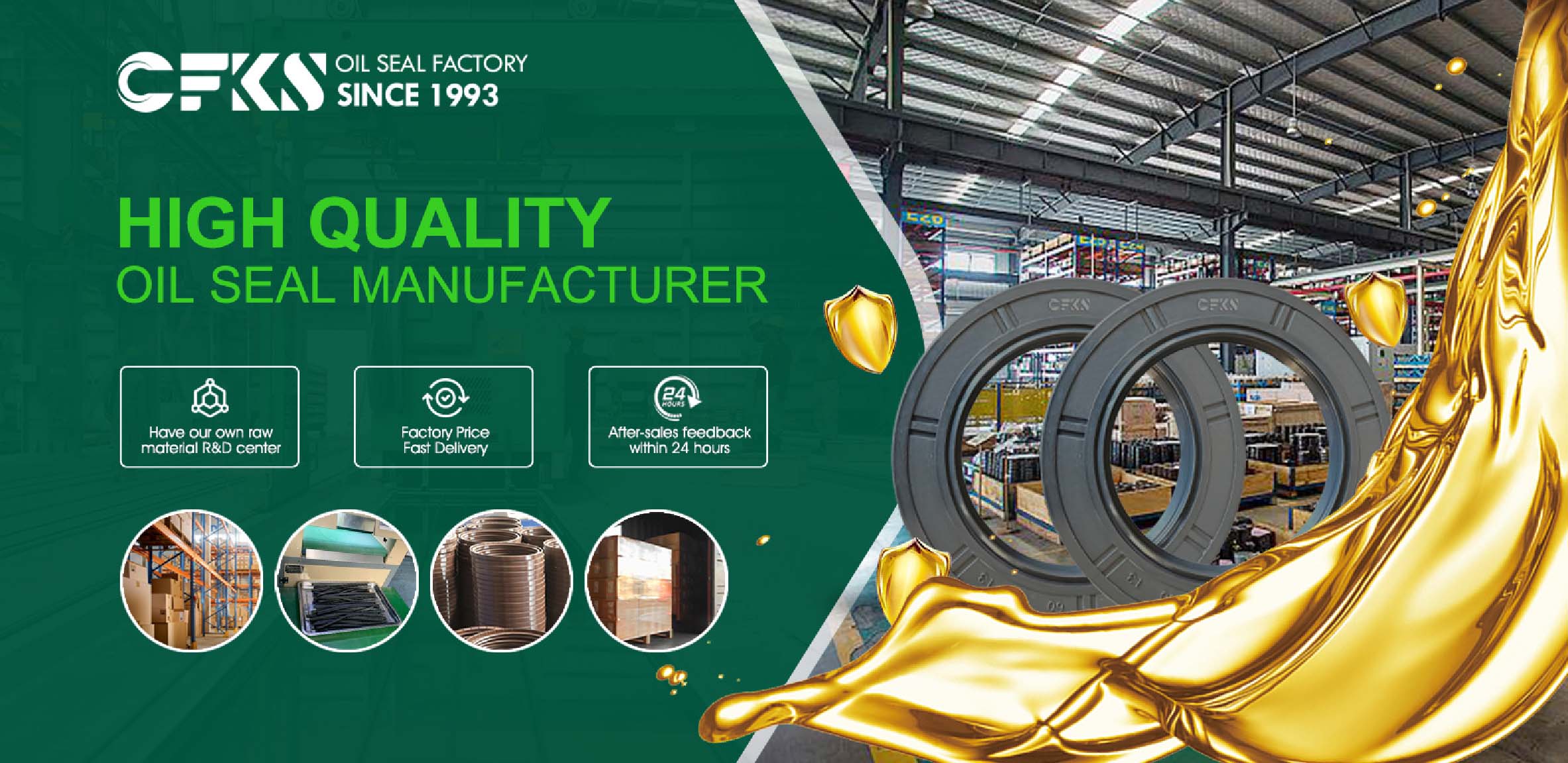